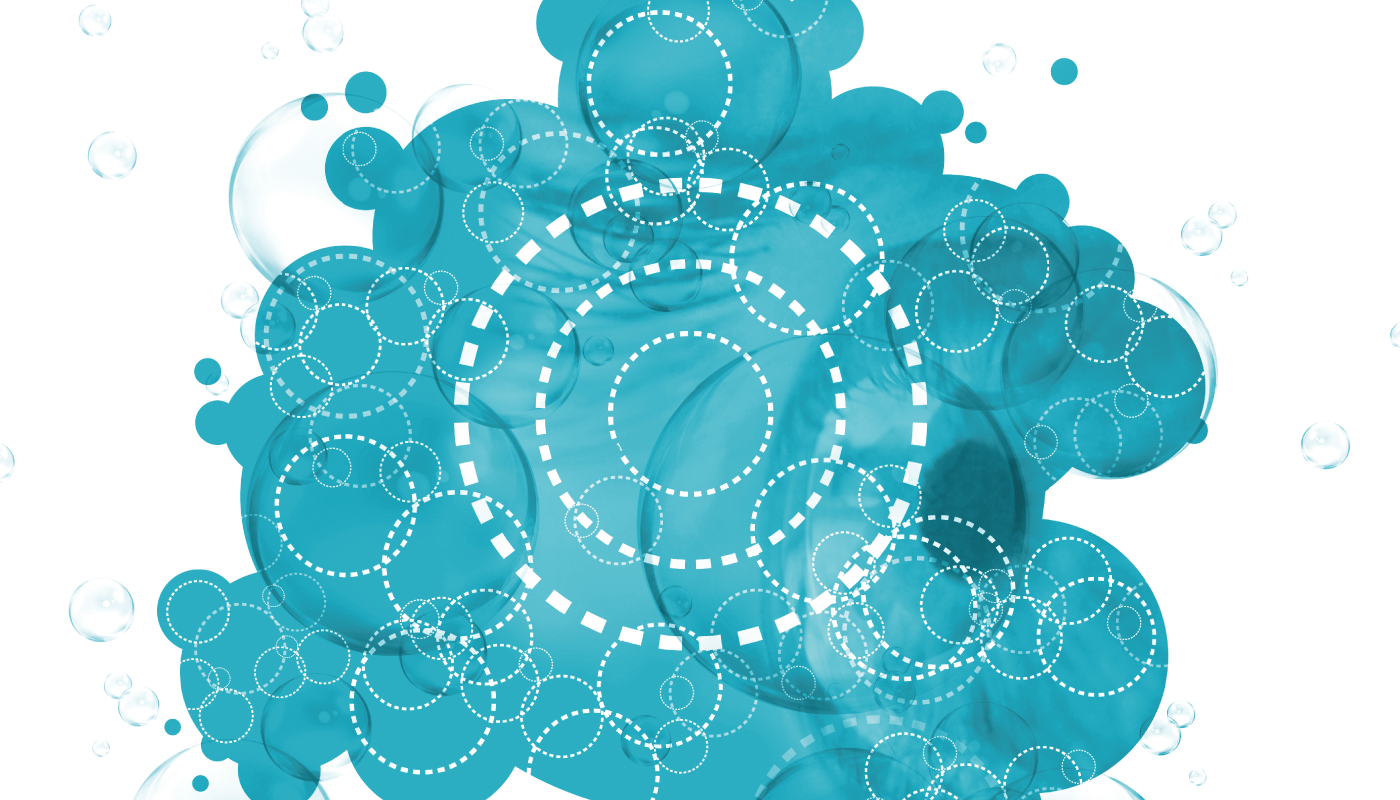
Intraocular lenses (IOLs) and specialist contact lenses have been around for years, with new designs released on a regular basis, but have you ever thought – really thought – how lenses are actually fabricated?
Let’s start by looking at the materials used to produce IOLs. These lenses were originally made out of silicone or, more commonly, poly(methyl methacrylate), or PMMA. PMMA is a rigid material widely used in transparent screening applications; for example, in aeronautics, aerospace, and electronics. You may know it by trade names such as Plexiglas or Perspex. Remarkably, this plastic came to ophthalmology by chance when Harold Ridley (of Rayner fame) discovered its biocompatibility properties after splinters of aircraft canopies were found in pilots’ eyes without subsequent infections. This breakthrough led to the development of implantable devices made of PMMA. Russia’s Fyodorov Eye Institute (MNTK) pioneered radical mass implantation surgical techniques for public health hospitals across the country, as well as in the UK’s National Health Service (NHS). These techniques brought affordable cataract surgery to thousands.
However, PMMA is a double-edged sword. Optically, it’s a great material. Its light transmission is high and its lathe machinability fantastic – but it is incredibly stiff, and so the race was on to develop a more flexible material that could eliminate radical invasive surgery, without compromising optical performance, therefore reducing patient recovery times: micro incision cataract surgery (MICS).
Softening an acrylic or making it flexible and suitable for micro incision techniques, can be done in two ways: by adding water-loving components to the matrix or by adding monomers that relax the matrix bonds. Hydrophobic and hydrophilic materials are commonly used and must be either machined or molded. For mass production of lenses, molding technology is preferable, but limits the range of powers and geometries available to those of the available mold insert. Machining (lathing and milling) enables specialist designs and customizations to be made for lower volumes or demands. The machining process is smaller in scale but no more complex than CNC machining operations in other industries. It starts with a material blank. These are usually 12.7- 15.0 mm in diameter and 2.5 to 3 mm thick (essentially the size of shirt buttons). These are usually formed from molded rods or, alternatively, “buttons in a bag” (a technique pioneered and developed by John McGregor OBE, founder of Contamac Ltd) in which a plastic envelope with cavities for each button is filled with acrylic monomer. Both rod and “button in a bag” methods are used for acrylics, which are thermally cured in temperature-controlled water baths (molded or semi-molded IOLs are UV cured). Because this is an exothermic process, the heat generated by the polymerization can run away with itself, so precise temperature control is vital to ensure that the resultant materials have the necessary properties, including: water potential for hydrophilic (22-26 percent), Tg (glass transition temperature) for hydrophobic, optical transmissibility, and refractive index. Most IOL materials also have UV blockers included as standard now. In addition, yellow dye can be added to act as a blue light filter, if required. Both these light wavelength ranges can have detrimental effects on longer term vision.
And the result…
The result is a rough, semi-transparent rod or button. It is often bent or misshapen, with menisci on each surface – certainly not in a fit state to become an IOL. This is because the polymerization process induces stresses within the material’s matrix. These stresses are so great the material warps and bends, so any residual stress needs to be removed, lest it adversely affects lens performance during the final lens machining process. A stress-relieving process is used on the material rods (annealing, a thermal process that relaxes the material), similar to that of metal alloys, such as steel or copper-nickel. Time and temperature profiles are tailored to each material to achieve final stability. For example, some materials are annealed in vacuum ovens to remove or draw out residual monomers within the newly formed polymer matrix. The hydration process that hydrophilic lenses undergo post-production, in the laboratory, also allows further residuals to be flushed out of the matrix.
In the case of a hydrophilic material, where the material is brittle and hard, machining is fairly easy. The process usually starts from rods being ground to a finish diameter (12–15 mm) and then salami-sliced to 2.5–3 mm thickness.
In the case of hydrophobic material, being softer than hydrophilic, machining poses significant challenges. Imagine attempting to machine a garden hose during a hot summer – not easy. Each materials manufacturer has its own technique to finish the raw material and generate a material blank with precise dimensions. These materials can also be plate-molded as the material is relatively soft at room temperature. The blanks can be cut out of the hydrophobic sheet with either a laser, a high-pressure water jet or mechanically with a punch or trepanned. The thickness of these blanks varies from one blank to another, because the polymerization causes shrinkage.
This material blank is now ready for shipping out to the specialist laboratories, who process the blank and generate a finished optical device. Care must be taken with shipping; a hydrophilic blank, as the name implies, “loves” water or moisture, so the environment must be controlled in special packaging and onward processing, or the material will start to hydrate before it is converted into a lens, causing incorrect geometries or off-target parameters.
From blank to block
What happens next? Once the material blanks are finished, they are distributed to the IOL laboratories who convert the seemingly simple “shirt buttons” into life-changing, sight-giving medical devices.
The lens generating process now happens. First the material blank needs to be held securely for machining, but not so tight the material is compressed. Compression can cause optical inaccuracies, so a blocking process can be used, bonding the material to a rigid arbor using wax. This arbor is held in the lathe by a collet, which holds the material stable. The wax acts as a bond, and the aim is to create a platform as rigid as possible in order to avoid any deformation in the material during machining.
This is fine for hydrophilic materials, but that doesn’t necessarily work with hydrophobic materials, as at lower temperatures the wax may become hard and brittle and lose its bond to the arbor. Here, an alternate method is used. As mentioned before, the material is soft and extremely difficult to machine at room temperature, therefore low temperature is needed, and the precise machining temperature is determined according to the glass transition Tg. When an amorphous polymer is heated, the temperature at which the polymer structure turns viscous, liquid or rubbery, is called the Glass Transition Temperature. It is also defined as a temperature at which the polymer takes on a characteristic glassy state with properties such as brittleness, stiffness, and rigidity (upon cooling). The Tg transition zone is critical and temperature ranges can be as low as -10 0C, although it varies.
Ice blocking is one answer for hydrophobic materials. Freezing arbors are used; they are interchangeable in order to fit various manufacturing steps. Generally, the arbor used for the first side is flat to fit the blank surface, while arbors for the second side are machined with a mirror image of the lens profile of side one. It’s a technique that requires expertise and skill. During machining, precise temperature control is needed. Special chill devices are used to control these low temperatures during lens processing, such as freeze plates or freeze chucks or maybe vortex chilled air devices.
A typical sequence includes spraying water on the blanks : positioning the blank on the frozen arbor. A few seconds later the water freezes and machining can begin.
Once you have finished, then what? You need to raise the temperature again. De-blocking the lens from the arbor is even easier, by reversing air flow from freezing to thawing on the devices.
Cutting geometries
The laboratories add value by design and manufacturing technique; each has its own patents with optics and brands, but many have a similar core material sources. So, after applying the design via the lathe software, or design software, the laboratories start to machine the lenses. This process can be split into five main sections: blocking the material, lathing the first side optics, milling the haptics, transfer blocking, and lathing the optics on side two. The machines used in these processes are the primary lens generators. They take the design in the form of a points file or point cloud, convert it to machine code, and cut the requested geometries. It may sound simple, but it’s not easy. Although the blanks may start at 2.5 to 3 mm thick, each one must be reduced to microns, if it is to pass through an injector cartridge via an incision size of 2 mm or less. The camel and the eye of a needle come to mind!
The lathe uses natural diamonds of various designs, shaping the geometries to get all of the features surgeons need – a square edge at the back of the optics, asphericity for aberrometric compensation, toricity, angulation, refractive zones, diffractive zones. Take toricity, which requires a special device on the lathe: by its nature, the toric zone needs to be exact. It is generated by having an oscillating tool synchronized with the rotation of the lathe’s air-bearing spindle and slides, a task performed by the axis’ encoders and positional feedback, together with bespoke software. The toric tool – also known as a fast tool – is a voice coil. In other words, it is a loudspeaker, but not one you can get music out of; instead, it produces a precise, non-rotationally symmetric surface, if a diamond tool is mounted on it. After all, toricity is shaped like a rugby/American football ball.
We now have optics on side one. The surface has been rough-machined and finished, a toric zone has been generated, and other geometric patterns and features have been added – a process that will have taken 3 to 5 minutes for most designs. The resulting disc looks like a mini spaceship. And it still needs its haptics cut – either on the lathe using a high-speed air-bearing milling spindle attachment or on a separate precision milling machine. There are advantages and disadvantages to both, depending on volume and production demands. If you mill haptics on the lathe, you don’t need to move the part from the original spindle collet position – so there’s no risk of transitional errors. However, when your machine is busy milling haptics, it’s not lathing optics. The choice, therefore, is for the production teams to determine. Whichever process you choose, the finish on the optics and haptics must be superb to avoid polishing (discussed in more depth later). Next up: side two.
The second side
You start by flipping the “burger” (transfer block) – a very important step, because you have to align side two to finish the optics correctly. The precision blocker is used again, with one arbor holding side one in place against the blocker and the second arbor mounted, ready to be blocked on top of your finished optics. The quality of the finished IOL depends on the precision alignment of the optical centers from both sides of the lens.
“Pouring hot wax over your lovely surface after all that?” I hear you cry. Yes! How else are you going to machine side two? At this point, the part-finished IOL has two arbors stuck to each side. Remove one by snapping it off. If you recoiled at the word “snap,” rest assured it is a little more precise than that. The arbor has to come off – but, without solvent or water to help, options are limited. When using an ice blocking system for hydrophobic materials, the difficulty lies in the fact the first side is released whilst simultaneously blocking the second side, without losing alignment with the arbor support. It is a complex process that needs to be reproducible and requires a lot of development and refinement.
Once side two is machined, you have a finished IOL. You can now de-block the lens and send it on to the metrology and inspection departments (which is another topic altogether!). If the lens is made from hydrophilic material, water is used to hydrate the lens to get to the 22-26 percent water content. The IOL will now have the texture of soft, squeezable candy.
Polish for a perfect finish?
Lathing rings (machining marks) have always been an issue when it comes to the perfect finish. With hydrophilic lenses, the manufacturer has an advantage in that they can use hydration. Most IOL hydrophilic acrylics have the aforementioned 22 to 26 percent water content, so have an expansion (or swell) factor of about 1.13. When the lens hydrates, some of the machining marks soften. Why not add more water and expand all the marks away? Well, adding too much water affects the mechanical properties of the lens. Remember, the lens has to be folded and squeezed through a micro surgical incision. The lens is under tremendous stress during this process and needs to be resilient enough to unfold without breakage or physical damage to the geometries of the design. Bear in mind that the sliding motion inside the cartridge could also damage the lens surface, so additives can be used to aid gliding during implantation. Using less water provides more resilience and is better for the smallest incision sizes, but effects foldability – or “unfoldability.”
The selection of water content is a compromise between foldability and mechanical properties. It is widely described in the literature that hydrophilic implants allow cells from the capsular equator to proliferate more easily towards the center of the posterior capsule. This phenomenon is called secondary cataract. Secondary cataract occurs as a normal consequence of the initial cataract operation. Also known as capsular fibrosis, it is the opacification of the natural lens envelope (the capsule) that is left in place during the operation to support the intraocular lens that has been inserted to replace the natural lens. Lenses made of hydrophobic acrylic, which are less sensitive to this type of proliferation, are therefore preferentially used. Although turning marks generally do not affect the optical resolution of the instrument, an unsmooth surface can cause stray reflections. So how do you eliminate this? The answer is tumble polishing.
In the polishing step, a receptable (jar) is charged with polishing beads, alumina, water, and other components, to adjust the pH of the slurry. The jar is agitated for a period of time to remove surface irregularities. Following the polishing step, the lenses are rinsed to clean the surfaces. This polishing step, even if carried out in hidden production time, requires a lot of handling and is a source of rejects.
Polish-free machining
There are also designs that cannot be subjected to this type of process. Yes, hard edges need to be smoothed to reduce the appearance of machining marks, but what happens to that lovely square edge or those sharp diffractive zones? They may blend away. So, what do you do when polishing could compromise the optical performance of your lens design?
Polish-free machining is the solution, but it brings its own issues – namely, time. Our lens has taken 5 to 10 minutes to machine; we need to double that to get a superfine surface finish without tumble polishing. The machinery technology or process may need to be reviewed or changed to achieve this level of precision, so time and capital investment are costs to consider for polish-free designs.
Meeting expectations
And what exactly is a “polish-free” surface? It’s a question that is asked many times in our industry. Some say, “I don’t polish, so it’s polish-free.” Others take a more pragmatic approach: “Surgeons don’t want to see machining marks on lenses during implantation, so we inspect lenses at the magnification they use.” Although that seems a more logical view, inspection is the last process in lens manufacture. Nobody wants to make rejects, so the answer lies at the beginning of this article – blocking and materials. The process as a whole needs to be reviewed from start to finish, to manage rejects at each stage and adjust process controls, such as diamond tool changes on the lathes, and mill and calibration routines, to reduce losses. Reject lenses mean costs.
Now machined, blocked, milled, lathed, and polished – or not! – inspected, packed and sterilized, your IOL is ready for implantation. The next time you watch an IOL unfold in front of your eyes, remember the path that brought it there. The miracle started long before you ever saw the lens. The teams of technologists – from materials scientists to process engineers, machinery suppliers to optical designers – are all part of your surgical team. For every lens you implant that saves or restores a patient’s sight, there is an army of technologists behind you – the secret of the perfect lens is what is behind it.
Plexiglas is a trademark of Arkema Group. Perspex is a trade name of Perspex International Ltd.