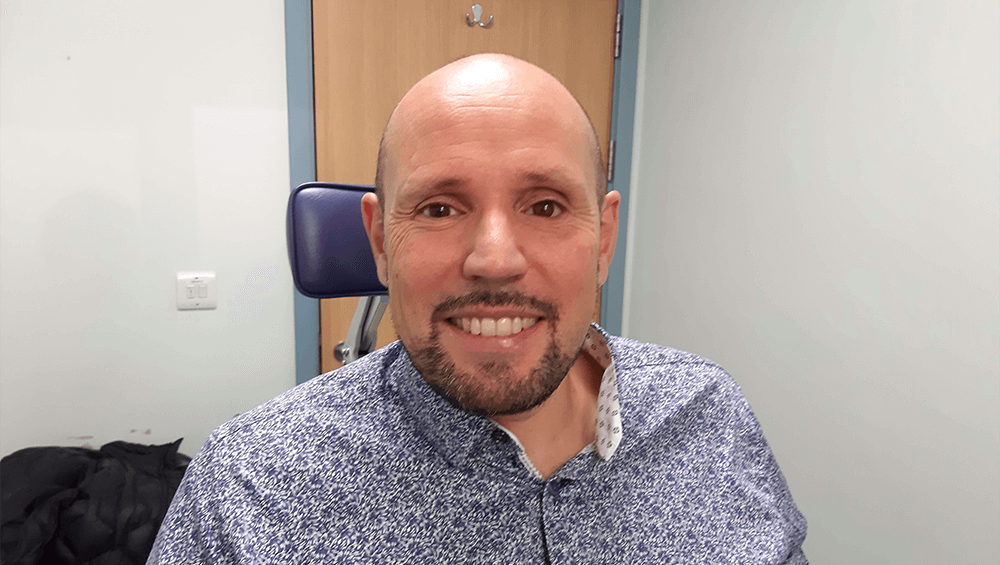
3D printing has been around since the 1980s, but it’s only relatively recently that it has become more accessible – both in terms of user-friendliness and cost. Today, researchers in multiple disciplines are incorporating 3D printing into project design. And, in the midst of COVID-19, it was even used to manufacture personal protective equipment.
But for Steve Verze, 3D printing is a very personal topic; thanks to the work of Mandeep Sagoo and his team at Moorfields Eye Hospital, UK, he is the world’s first recipient of a fully 3D printed prosthetic eye (1).
Steve’s story is a fantastic example of how 3D printing can benefit both the patient and medical services. Using digital mapping from a scan of Steve’s eye socket, his 3D printed prosthetic eye is truly personalized, which means a precise – and comfortable – fit. And it looks as natural as possible thanks to digital scans of the good eye.
And that’s all great news. But what’s equally impressive is the turnaround time. The digital scans are sent to Germany for the 3D printing process, which is completed in under three hours. After printing, the eye is sent for finishing and fitting back to the UK– the whole process only taking two to three weeks.
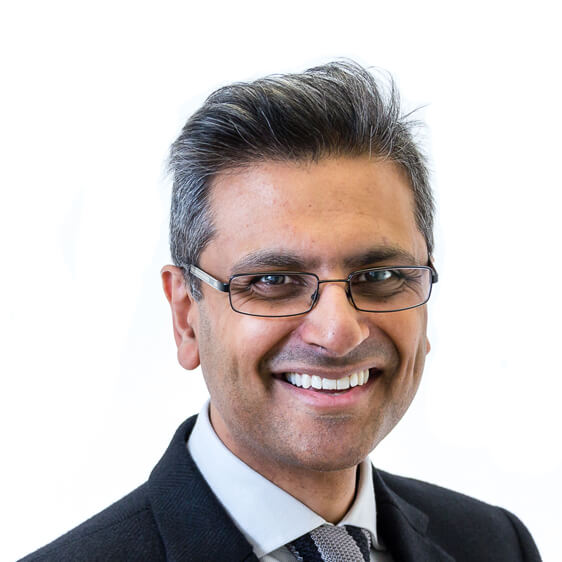
Previously, a temporary prosthetic eye would be given to a patient following surgery for six weeks to allow for healing, but this would not be a precise match for their natural eye and could cause anxiety for the patient. The wait for a moulding appointment for a more suitable prosthetic would then take four to five months, with the actual moulding process being extremely invasive and difficult; children require general anesthetic for the procedure.
It’s early days, but with widespread adoption of technology for 3D printed eye prosthetics, the timeline for production could be reduced further – imagine how happy patients would be if their ophthalmologist could assess, scan, and print a prosthetic for fitting in a single day…
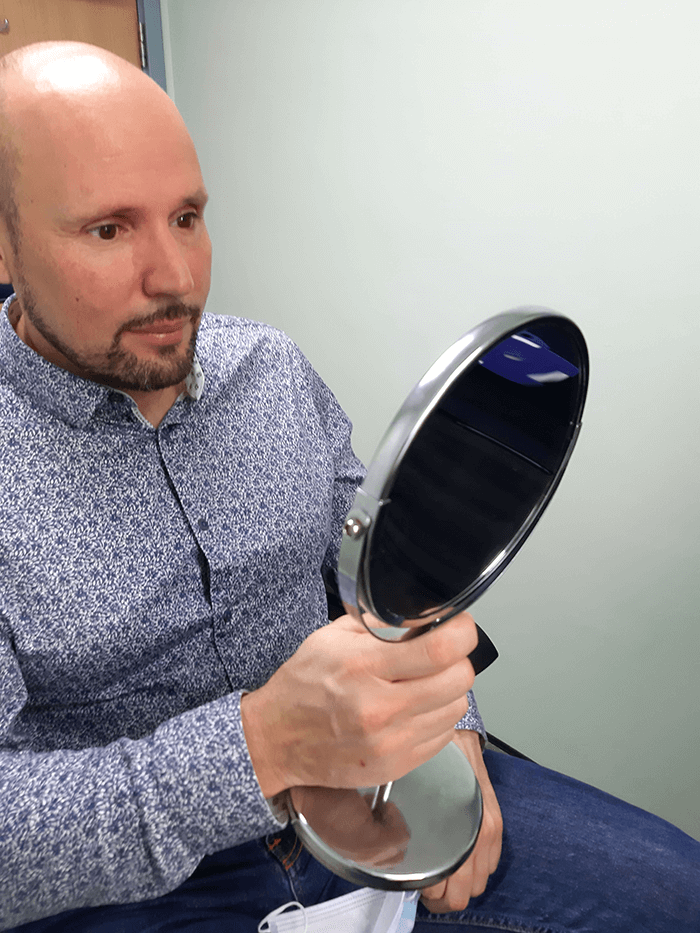