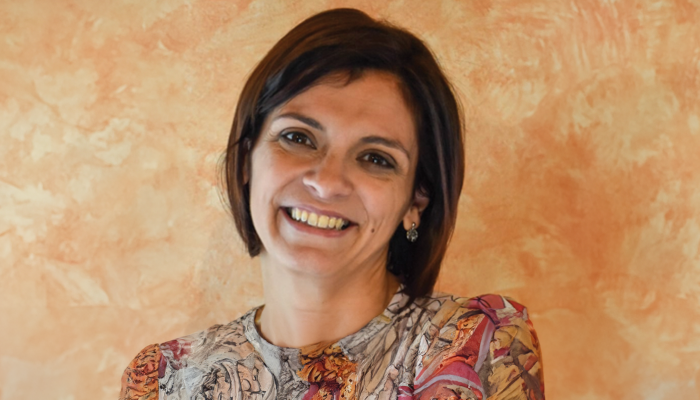
Headshot supplied by Vincenza Pironti
The ophthalmic drug delivery market is increasing – valued at $12.1 billion in 2021 and projected to reach $23.4 billion by 2030 (1).
The most common ophthalmic container format is ocular multi-dose, with a 72.1 percent revenue share of the ophthalmic packaging market in 2022 (2). Multi-dose containers are typically 10–15 mL and are designed for multiple uses over a prolonged period, rather than single-use.
Recent events, however, have pointed to potential challenges when using multi-dose containers. Products have been recalled due to microbial contamination, caused by cracks forming in multi-dose filter caps after excessively prolonged use (3). Also, multi-dose preservatives, such as benzalkonium chloride (BAK), can induce burning and itching over time (4).
Ophthalmic drug developers are turning to unidose container formats to overcome these challenges and deliver safe and effective treatments to their patients. Blow-fill-seal (BFS) technology is a promising alternative container format for pharmaceutical and biotech companies developing sterile ophthalmic therapies.
The eye’s sensitivity necessitates stringent sterility and safety requirements for ophthalmic drug products and container systems. Aseptic fill and finish are required to prevent microbial contamination, which can lead to eye infections, as well as to avoid particulate contamination, which can irritate or damage the eye. Ophthalmic containers must maintain product sterility and prevent leakage and contamination throughout the product lifecycle to ensure product safety.
Used for aseptic filling or terminally sterilized liquid products, BFS is an automated manufacturing technique; the unidoses are formed, filled with product, and sealed in continuous, integrated, automatic operation – very unlike the manufacturing process multi-dose filling, which requires multiple components, including glass vials, caps, plastic bottles, and filters. The BFS process occurs in a sterile, enclosed area inside the BFS line without human intervention – and it avoids the need to store, wash, dry, and sterilize multiple components, improving the cost-effectiveness and production efficiency of BFS compared with multi-dose.
BFS unidose is suitable for solutions, gels, suspensions and emulsions, and even sensitive biologics. However, developing BFS products requires close consideration of development and manufacturing processes, including formulation development, analytical services, and product filling. Contract development and manufacturing organizations (CDMOs) can provide these services at pilot and commercial scale, supporting developers wishing to explore the BFS manufacturing process.
With access to these alternative container formats, drug developers can boost their ophthalmic products in the growing market – and deliver convenient and effective treatments to patients.
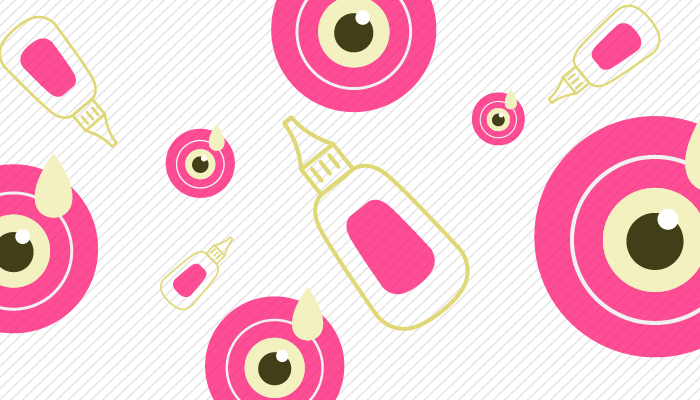