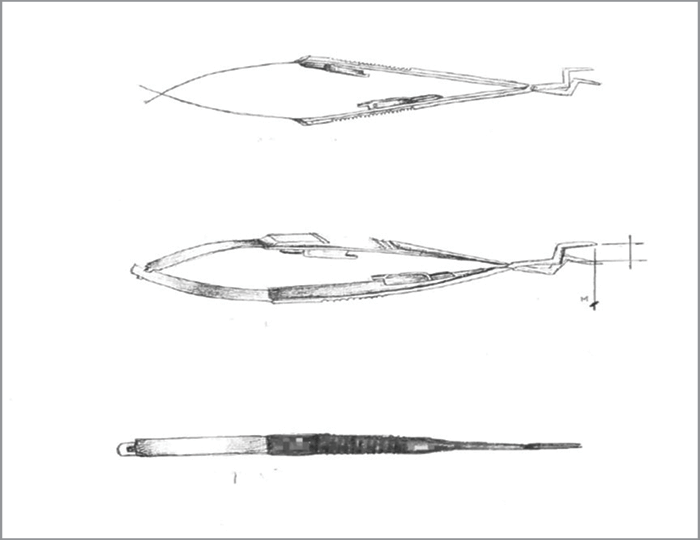
With the advent of 3D printing comes almost infinite possibility. Household items, artificial limbs, and even concept cars... What can’t be manufactured by these marvelous machines? But the world of 3D printing isn’t only about creating increasingly impressive items. The potential to get from page to product in just a few clicks has led many inventors to embrace the technology for rapid prototyping. And eyecare is no exception. Here, Donny Suh, a pediatric surgeon and keen inventor from the University of Nebraska Medical Center (UNMC) and Children’s Hospital and Medical Center, shares how he developed an improved version of a tool commonly used in pediatric strabismus surgery.